Machine Control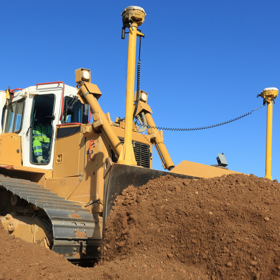
Often an engineer will be the conduit between a designer and a machine operator. Until now the machine control system has very much dictated what kind of data the engineer will be expected to provide.
A 3D DTM is usually called-for which, in many people's experience, is simply a set of triangles in a DXF or LandXML file. But if you're grading a bund or reprofiling a track it's so much more efficient for the data to also include the breaklines or links as alignments which can then be followed by the machine operator. And that's where LSS helps. By including such information in the exported model from LSS the engineer has regained control over the process and can check the integrity of the data so much more easily. This results in efficiency savings and when the data is fed back into LSS he can compare the as-built with the design.
What can LSS do for you?
- Import 3D designs in a variety of formats
- Instantly model the terrain surface and “flag up” any anomalies in that data
- Make amendments to the design, compare volumes with Original Ground models and report the results by depth bands, zones, material types, phases of the job etc...
- Design your own earthworks
- Add depths so you can determine the earthworks outline (base of a road, building, channel, capping layer, liner etc)
- Visualise in 3D to check for mistakes and also for presentations
- Draw sections (profiles) through multiple models
- Export the required design to Machine Control in the most appropriate format for the system - DTM and linework in LandXML, DXF or CSV. Systems include Trimble Earthworks, Leica Icon, Topcon
- Include material depths (formation models)
- Include alignments for the machine operator to follow
- Re-import the 'as built' data for comparison of levels and volumes
- Generate a 'level difference' model (isopachytes) to compare the two
Recommended product for this work: LSS Elite
Preparing your data for export to Machine Control (formation levels)
Exporting to Machine Control